Drive Motor Development Trend / Oil Cooling, Hair-pin, Integration
Apr 18, 2023
Reading Volume :
With the rapid development of the new energy vehicle industry, higher requirements are put forward for the performance of the drive motor, such as peak power, operating efficiency, response speed and vibration noise, so the drive motor is gradually moving towards oil cooling, flat wire, All-in-one integration.
Drive Motor Oil Cooling
Oil cooling can directly contact the inside of the drive motor and is the preferred heat dissipation method. The driving motor cooling system can be mainly divided into two categories: air cooling and liquid cooling. Air-cooled heat dissipation uses air as the cooling medium and dissipates heat through air convection. It has a simple structure, low cost, and convenient operation and maintenance, but the cooling effect is average, and it is mainly used in electric vehicles with low power levels. Liquid cooling can be divided into cooling water and oil. Water cooling has low cost and no pollution. However, due to the need for internal insulation of the motor, water cooling can only dissipate heat in the water jacket on the outer wall of the motor casing; while oil cooling is because of its good Insulation, it can directly conduct contact heat dissipation inside the motor, and the effect is better, so it is also the first choice for heat dissipation of the drive motor.
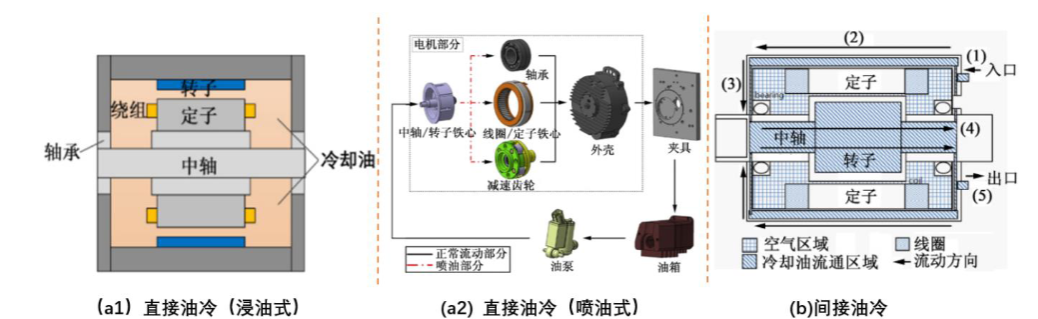
Motor oil cooling
Indirect oil cooling through the hollow motor shaft is even better. Oil cooling can be divided into direct oil cooling and indirect oil cooling according to whether the internal electromagnetic wire winding and other parts are cooled. There are two types of direct oil cooling: oil immersion and oil injection. The oil immersion type uses the insulating properties of the oil to directly pass the oil into the motor and immerse the stator and rotor. This method can effectively enhance the heat transfer coefficient inside the motor, but the immersion The oil type will cause the rotor to rub against the oil during operation, reducing the efficiency of the motor; the oil injection type is to use the oil pump to spray the transformer oil onto the fixed blade designed on the rotor, and through the rotation of the blade, the transformer oil will be splashed to the stator winding of the motor The parts such as the end are cooled. The indirect oil cooling is that the cooling oil circulates and dissipates heat through the hollow motor shaft and the motor outer shell, which can directly remove the internal heat of the motor, and has less friction loss with the rotor, which has obvious advantages.
Drive motor Hair-Pin
The demand for high power and the arrival of scale effect will make the Hair-Pin motor become the mainstream of the industry. In the past, most of the magnet wires for driving motors were round copper wires. Since the requirements for round wire accuracy and other aspects are relatively low, and manual labor can be used for small batches, the economy is relatively good. With the advent of the era of new energy vehicles, motors are gradually moving towards high power and high speed, and the requirements for the working efficiency of motors are getting higher and higher. Therefore, Hair-Pin motors are becoming the mainstream of the industry, and the penetration rate of flat wire motors has reached 27% in 2021. , with the further improvement of the scale effect of the motor industry, Hair-Pin motors will continue to penetrate rapidly.
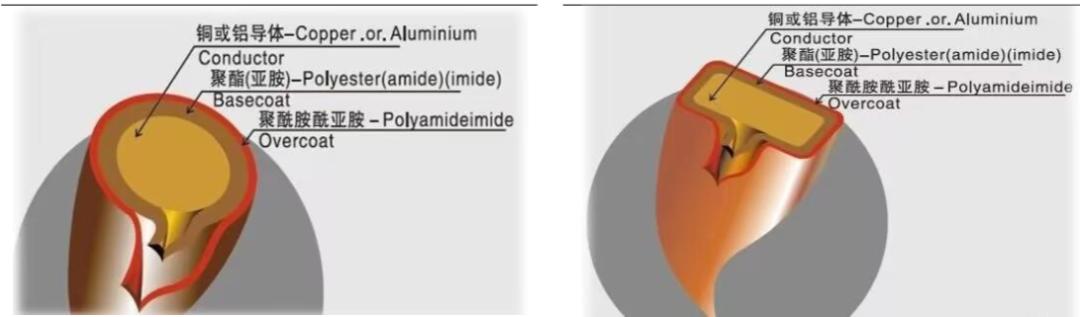
(Left): Schematic diagram of round wire structure (Right): Schematic diagram of flat wire structure
The Hair-Pin motor has a higher full slot rate and better driving efficiency.The biggest difference between Hair-Pin and round wires is that the cross-sections of the two are different. The magnet wire windings composed of round wires have a lower full slot rate, while the electromagnetic wire windings composed of Hair-Pin have smaller gaps and higher slot fill rates. According to relevant information statistics, in the same space, the Hair-Pin motor can be filled with 20% to 30% more wires, which can increase the slot filling rate by about 20%, so that the maximum efficiency of the whole machine can be increased by about 2%. At the same time, it can also be found that the use of Hair-Pin motors has a larger high-power range, which is more friendly to battery life.
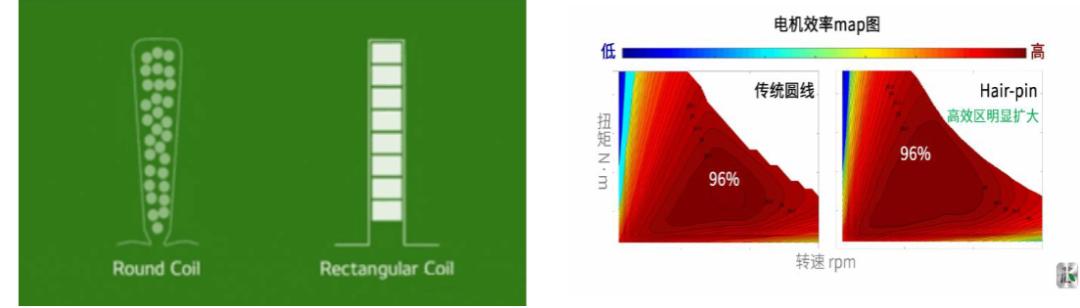
(Left): Distribution diagram of conductor interface of round wire motor and flat wire motor (Right): Thermal simulation structure of round wire motor and flat wire motor
Drive motor all-in-one integration
The electric drive system has obvious advantages and is in line with the current development trend. The all-in-one electric drive system refers to the integration of drive motors, motor controllers, reducers, DC converters, on-board chargers, high-voltage power distribution boxes and other components, and the sharing of housing wiring harness and other components to achieve lightweight and lower cost. cost and higher efficiency. After the integration of the electric drive system, compared with the original distributed system, the volume will be reduced, saving space in the car, which is conducive to the modular design of car companies, reducing costs and increasing efficiency. At the same time, taking the three-in-one with more integration on the market as an example (that is, drive motor + motor controller + reducer), the integration can share oil cooling and heat dissipation, and the lubricating oil in the reducer can serve as the cooling oil in the motor, which has more advantages obvious.
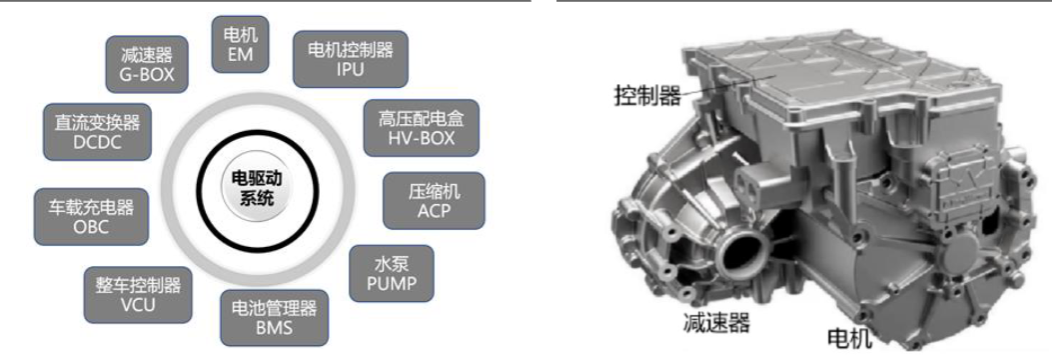
(Left): Integrated components of electric drive system (Right): Three-in-one electric drive system
Drive Motor Oil Cooling
Oil cooling can directly contact the inside of the drive motor and is the preferred heat dissipation method. The driving motor cooling system can be mainly divided into two categories: air cooling and liquid cooling. Air-cooled heat dissipation uses air as the cooling medium and dissipates heat through air convection. It has a simple structure, low cost, and convenient operation and maintenance, but the cooling effect is average, and it is mainly used in electric vehicles with low power levels. Liquid cooling can be divided into cooling water and oil. Water cooling has low cost and no pollution. However, due to the need for internal insulation of the motor, water cooling can only dissipate heat in the water jacket on the outer wall of the motor casing; while oil cooling is because of its good Insulation, it can directly conduct contact heat dissipation inside the motor, and the effect is better, so it is also the first choice for heat dissipation of the drive motor.
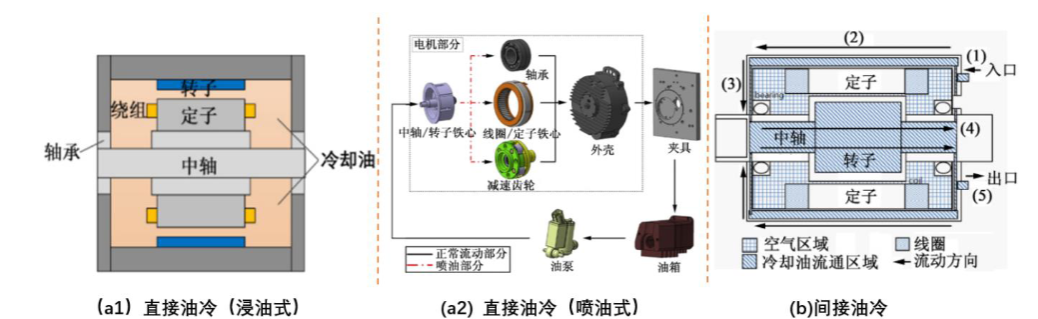
Motor oil cooling
Indirect oil cooling through the hollow motor shaft is even better. Oil cooling can be divided into direct oil cooling and indirect oil cooling according to whether the internal electromagnetic wire winding and other parts are cooled. There are two types of direct oil cooling: oil immersion and oil injection. The oil immersion type uses the insulating properties of the oil to directly pass the oil into the motor and immerse the stator and rotor. This method can effectively enhance the heat transfer coefficient inside the motor, but the immersion The oil type will cause the rotor to rub against the oil during operation, reducing the efficiency of the motor; the oil injection type is to use the oil pump to spray the transformer oil onto the fixed blade designed on the rotor, and through the rotation of the blade, the transformer oil will be splashed to the stator winding of the motor The parts such as the end are cooled. The indirect oil cooling is that the cooling oil circulates and dissipates heat through the hollow motor shaft and the motor outer shell, which can directly remove the internal heat of the motor, and has less friction loss with the rotor, which has obvious advantages.
Drive motor Hair-Pin
The demand for high power and the arrival of scale effect will make the Hair-Pin motor become the mainstream of the industry. In the past, most of the magnet wires for driving motors were round copper wires. Since the requirements for round wire accuracy and other aspects are relatively low, and manual labor can be used for small batches, the economy is relatively good. With the advent of the era of new energy vehicles, motors are gradually moving towards high power and high speed, and the requirements for the working efficiency of motors are getting higher and higher. Therefore, Hair-Pin motors are becoming the mainstream of the industry, and the penetration rate of flat wire motors has reached 27% in 2021. , with the further improvement of the scale effect of the motor industry, Hair-Pin motors will continue to penetrate rapidly.
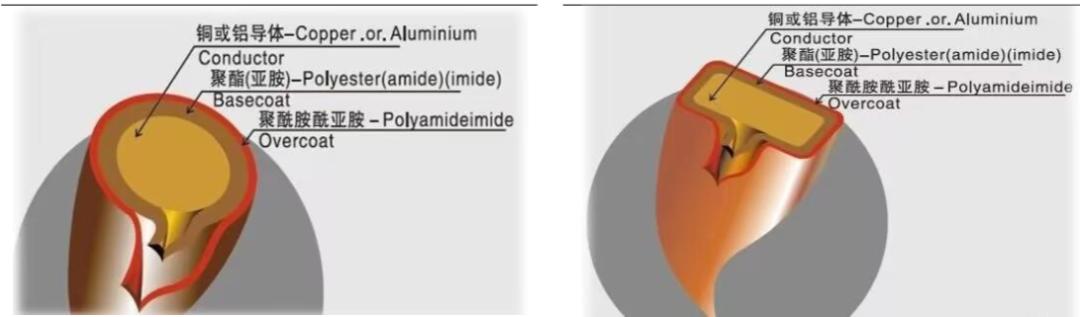
(Left): Schematic diagram of round wire structure (Right): Schematic diagram of flat wire structure
The Hair-Pin motor has a higher full slot rate and better driving efficiency.The biggest difference between Hair-Pin and round wires is that the cross-sections of the two are different. The magnet wire windings composed of round wires have a lower full slot rate, while the electromagnetic wire windings composed of Hair-Pin have smaller gaps and higher slot fill rates. According to relevant information statistics, in the same space, the Hair-Pin motor can be filled with 20% to 30% more wires, which can increase the slot filling rate by about 20%, so that the maximum efficiency of the whole machine can be increased by about 2%. At the same time, it can also be found that the use of Hair-Pin motors has a larger high-power range, which is more friendly to battery life.
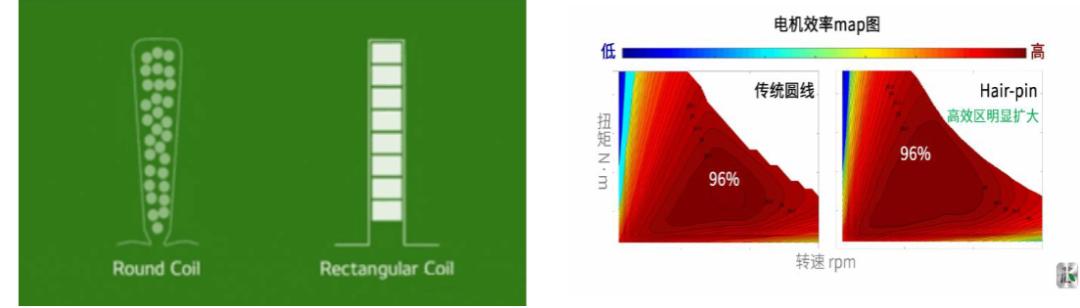
(Left): Distribution diagram of conductor interface of round wire motor and flat wire motor (Right): Thermal simulation structure of round wire motor and flat wire motor
Drive motor all-in-one integration
The electric drive system has obvious advantages and is in line with the current development trend. The all-in-one electric drive system refers to the integration of drive motors, motor controllers, reducers, DC converters, on-board chargers, high-voltage power distribution boxes and other components, and the sharing of housing wiring harness and other components to achieve lightweight and lower cost. cost and higher efficiency. After the integration of the electric drive system, compared with the original distributed system, the volume will be reduced, saving space in the car, which is conducive to the modular design of car companies, reducing costs and increasing efficiency. At the same time, taking the three-in-one with more integration on the market as an example (that is, drive motor + motor controller + reducer), the integration can share oil cooling and heat dissipation, and the lubricating oil in the reducer can serve as the cooling oil in the motor, which has more advantages obvious.
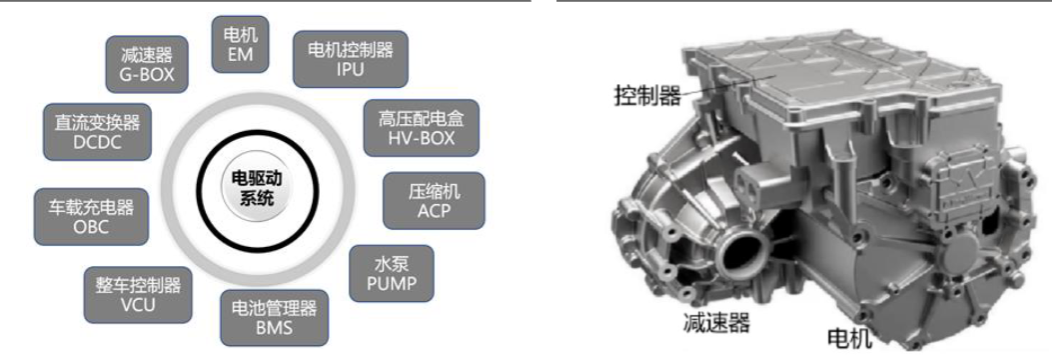
(Left): Integrated components of electric drive system (Right): Three-in-one electric drive system